Induction motors have been the workhorse for industrial and commercial pumping for over a century. They still make up the vast majority of all application installations. They are reliable, require relatively little maintenance and offer efficiencies in most cases over 90%. With new rules from the United States Department of Energy, in a few years, super premium (similar to IE4) efficiency will be required for induction motors from 100 to 250 horsepower. So, why is there so much discussion and momentum in the market for synchronous motors?
Synchronous motors have many names in the market, including electronically commutated motors (ECMs), brushless direct current motors (BLDCs), brushless permanent magnet (BPM) motors and others. The goal of this article is to review the general advantages and disadvantages of choosing a synchronous motor for an application versus sticking with induction. The assumption is the application is already running variable speed, or will soon be converted to variable speed, and now the motor technology to drive the application is being considered. Wireless Angle Sensor

The first topic to consider is VFD selection. Most pumping applications are variable torque. For induction motor driven variable torque pumping systems, scalar or volts per hertz VFDs can be utilized. Volts per hertz VFDs are the simplest, and in most cases the most cost-effective, VFDs on the market. Though some synchronous motors can utilize volts per hertz VFDs, most synchronous motors require a more advanced VFD that is capable of vector control. Volts per hertz and vector control VFDs are commonly available on the market, but vector control VFDs are typically more expensive and require more input at setup.
The second topic to consider is VFD setup. VFD setup for a volts per hertz VFD is normally simple. Also, most VFDs for induction motors have an auto-tune or auto-setup function that works well with induction motors. Synchronous motors typically require more setup functions.
Additionally, an auto-tune function rarely works effectively on synchronous motors. The more advanced setup process for a VFD with a synchronous motor should not be a large burden, but getting input from the motor and/or VFD manufacturer on how to set up the VFD for a specific synchronous motor is important. The other solution is to purchase a set of motor and VFD, or an integrated motor and VFD that is already pre-set.
The third topic is system efficiency. System efficiency is where synchronous motors shine. Though induction motors can be acquired with IE4 or super premium efficiency levels, the full load efficiency of an induction motor drops off at lower speeds much faster than for synchronous motors. Synchronous motors have virtually no rotor losses. Increased rotor losses at lower speeds are a major contributor to lower efficiencies for induction motors at slower speeds (and lower loads for variable torque applications). Synchronous motors are typically IE4, or even IE5, at full load efficiency and maintain that efficiency better across a broad speed range.
Though the full load efficiency for different synchronous motor technologies can vary, the higher part load efficiencies are consistent across different technologies, as they all have virtually no rotor losses. Another advantage of synchronous to induction motors is that typically the synchronous motor can attain higher efficiencies in mechanical packages that are consistent with current induction premium efficient motor designs, or sometimes in even smaller sizes. Higher efficient induction motors typically require more active material and are sometimes in longer frames, which can cause fit and form issues with current installations.
The fourth topic is operation stability. Induction motors are robust, not just in manufactured process but also in operation. They create torque until a fairly high stall level. They also have the capability to continue to run even when the load speed fluctuates. An induction motor runs at a speed less than the synchronous speed. The reduced speed differential is called motor slip and is represented by a percent.
In a typical premium efficient motor, that slip percent is about two to three percent. That small percent of speed acts almost as a buffer between the pump load and the VFD. Even in somewhat unstable operating conditions, an induction motor on a VFD will “ride through” many disruptions from conditions such as limited water hammer or an aggressive reduction in speed. A synchronous motor does not have that buffer, as the motor is running at synchronous speed. Any disruption in the load speed can cause issues, including desynchronization or a possible trip of the VFD on overvoltage of the direct current (DC) bus.
In the case of a desynchronization, some systems can recover and the motor can resynchronize. If the motor stays out of synchronization, in most cases, the system will trip on overcurrent or may stop running altogether. The VFD can be set up to handle a situation like this, but it must be planned for and programmed to be able to recover without a person’s intervention.
When a system speed decreases quickly, the motor may be put into an overspeed condition. That is rare for an induction motor, but it can occur. It is more common for a synchronous motor, as it is already at the limit while operating normally. If either motor technology ends up running faster than the VFD is attempting to control it to, the motor will generate power back to the VFD for a short period. That can cause the VFD to trip, typically on overvoltage. Again, the VFD can be set up for this occurrence. Sometimes this can be accommodated via VFD settings, but in some cases a resistor can also be added to the VFD to capture the voltage and protect the VFD. This sounds complicated, but the VFD manufacturer in many cases can assist in setting up the VFD to handle this and other application considerations for the synchronous motor.
The fifth topic is motor and VFD replacement. A few years ago, this would have been a significant issue for the industry attempting to apply synchronous motors on VFDs. Now, it is becoming less of an issue as more synchronous motors, both standalone and integrated with VFDs, enter the market and are becoming stock items. Also, more VFDs are capable of running synchronous motors, with more VFD manufacturers gaining application experience with synchronous motors.
That said, it can still be an issue. A local motor and VFD distributor is going to carry a broad set of induction motors and VFDs for local replacements. If synchronous motors are installed, it is recommended an investigation of stock replacements be made early on during the installation process. Also, many stock VFDs are now capable of being set up to run a synchronous motor. That setup process, as discussed in topic two, can be a challenge, but the situation can be planned for to overcome any issues.
Induction motors and synchronous motors are both great selections for variable speed applications in the pump industry. Synchronous motors have a significant advantage in system efficiency and therefore are growing in popularity to lower total power use and aid in the reduction of carbon emissions. Care and thought must occur when synchronous motors are chosen for pump applications. The trends in the industry will continue to make synchronous motor applications simpler and more supported than ever.
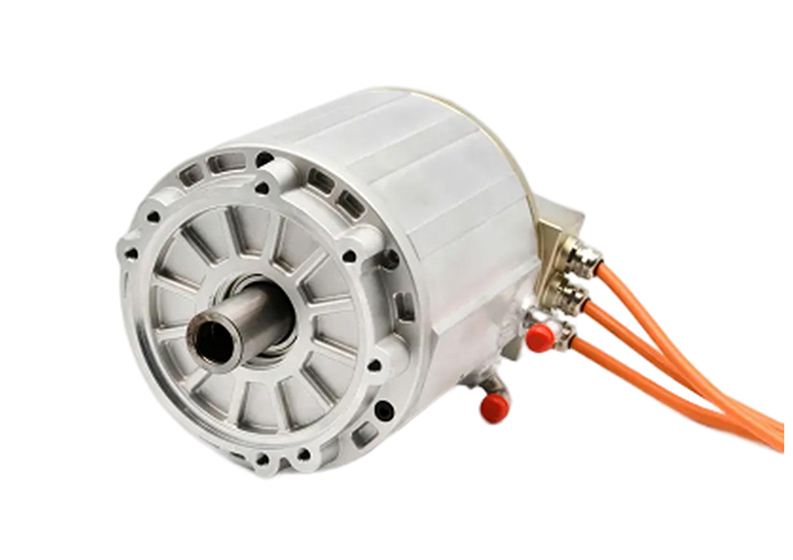
Single Phase Motor Vfd Drive Tim Albers is director of product management for Nidec Motor Corporation/U.S. Motors. For more information, visit www.nidec.com.